Table of Content
1 What Industries Use Quality Management
2 Industries That Can Benefit from QMS Software
Life Sciences (Pharmaceuticals & Biotechnology)
Medical Device Manufacturing
Automotive and Aerospace Manufacturing
Food & Beverage Manufacturing
Other Industries and Emerging Sectors
8 How to Choose QMS Software That Meets Your Industry Demands
Additional Considerations (Industry-Specific):
Shortlisting and Evaluation Process: With criteria in hand, the process might involve:
11 Cost Considerations and ROI of QMS Software Based on Industries
12 Implement the Best QMS Software for Your Industry with Qualityze
13 Conclusion
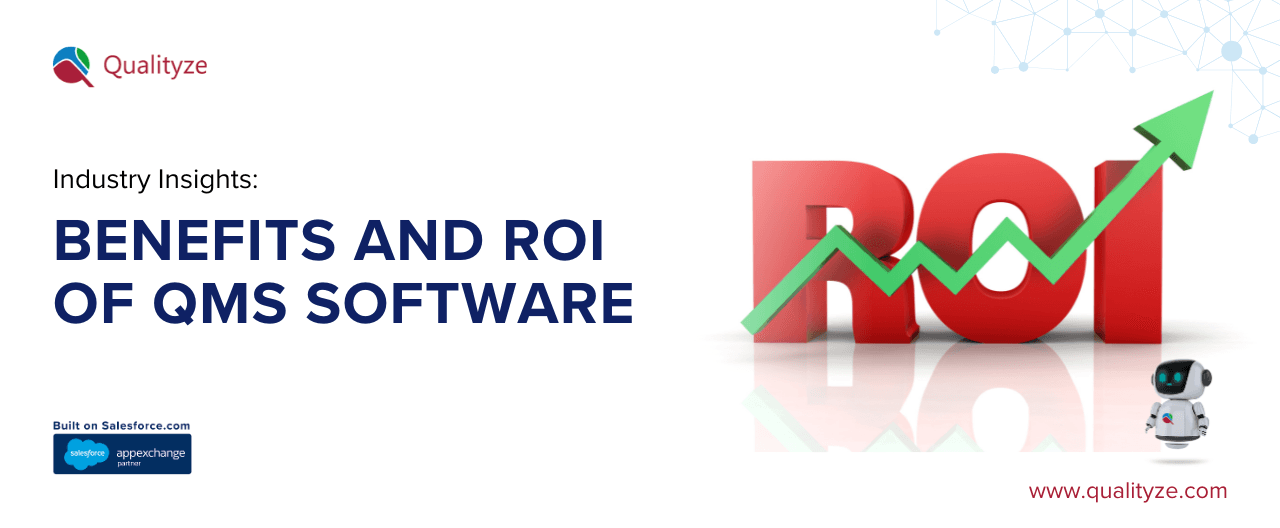
Quality Management Systems (QMS) are formal frameworks of processes and procedures aimed at ensuring product quality, safety, and regulatory compliance across organizations. Originally rooted in manufacturing, QMS principles are now applied in virtually every industry from production lines to service sectors. In fact, “quality management systems offer benefits for nearly every industry, from manufacturing to the government sector.”
Globally, the ISO 9001 standard for QMS has over 900,000 certified organizations covering ~1.3 million sites , underscoring the widespread adoption of quality practices. Certain industries, however, derive exceptional value or even require QMS implementation due to stringent regulatory demands and high stakes for product/service failures. This outline explores the key industries that benefit most from QMS software – with a focus on regulated manufacturing sectors (notably life sciences and medical device manufacturing in North America, the EU, and Germany) – and provides guidance on selecting and implementing QMS software with cost considerations and ROI.
What Industries Use Quality Management
Quality management has deep roots in manufacturing industries. Sectors like automotive, aerospace, electronics, and industrial goods have long used QMS frameworks (e.g., ISO 9001) to minimize defects, reduce waste, and ensure consistency. Manufacturers must coordinate diverse operations to deliver quality products, and “the cost of a mistake can be extremely high” – thus QMS helps manage risks and improve process control . For example, the automotive industry’s QMS standard (IATF 16949) builds on ISO 9001 and is often mandated by major car OEMs for their suppliers
Over time, the use of QMS has expanded beyond manufacturing. Healthcare providers (hospitals, labs) adopt QMS to improve patient care outcomes and comply with accreditation requirements
Universal Need, Critical for Some - while quality management started as a competitive practice, it has become a universal business function. Every industry that values customer satisfaction and operational excellence can leverage QMS, but the benefit is particularly pronounced in regulated industries where QMS ensures compliance and prevents high-impact failures. This sets the stage for examining which industries benefit most from dedicated QMS software solutions, which digitize and streamline these quality processes.
Industries That Can Benefit from QMS Software
Life Sciences (Pharmaceuticals & Biotechnology)
Pharmaceutical and biotech companies operate under some of the strictest regulations because product quality directly affects patient safety. Firms must comply with FDA current Good Manufacturing Practices (cGMP) in the U.S. and EMA guidelines in the EU. A digital QMS:
-
Improves Batch Release and Throughput: Automates documentation and reduces manual bottlenecks.
-
Enhances Change Management and Traceability: Essential when handling thousands of production records.
-
Ensures Data Integrity: Supports compliance with FDA 21 CFR Part 11 (electronic records, validation, access controls).
These capabilities protect patient safety and help companies maintain the licenses they need to operate.
Medical Device Manufacturing
Medical device firms are subject to strict regulatory requirements, including FDA’s 21 CFR Part 820 in the U.S. and the EU’s MDR along with ISO 13485 certification.
-
Streamlined Compliance: QMS software helps firms stay inspection-ready.
-
Improved Product Quality: It integrates design control, risk management, and supplier quality, ensuring that processes meet global standards.
-
Faster Market Access: A digitized QMS can expedite the CE marking process in Europe.
For device manufacturers, efficient quality systems translate into competitive advantages and quicker time-to-market.
Automotive and Aerospace Manufacturing
While not regulated for public health, automotive and aerospace products are safety-critical and demand stringent quality standards.
-
Automotive: Compliance with IATF 16949 is nearly mandatory for suppliers. QMS software helps catch issues early in the supply chain, reducing defects and warranty claims.
-
Aerospace: Adherence to AS9100 and other standards ensures rigorous documentation and configuration management. This reduces disruptions and helps meet regulatory audits (FAA/EASA).
Overall, robust QMS software leads to fewer production disruptions, lower warranty costs, and improved operational efficiency.
Food & Beverage Manufacturing
The food and beverage sector must comply with regulations such as the FDA Food Safety Modernization Act (FSMA) in the U.S. and various EU food safety directives.
-
Ensuring Safety and Compliance: QMS software manages critical control points (CCPs) and maintains traceability records.
-
Rapid Recall Management: In case of contamination or mislabeling, a digital system enables swift, targeted recalls—potentially avoiding recalls costing $10–30+ million.
-
Enhancing Brand Reputation: Consistent quality supports consumer trust in a competitive market.
Other Industries and Emerging Sectors
Industries such as electronics, high-tech manufacturing, chemicals, and laboratories benefit from QMS software by ensuring process consistency and data integrity. Even emerging fields like regulated cannabis production use QMS to navigate evolving standards. Essentially, any industry that seeks to reduce errors and improve process efficiency can benefit from a robust, digital quality management system.
A summary table below highlights key industry standards and quality needs:
Industry |
Key Standards/Regulations |
Focus Areas |
Life Sciences |
FDA cGMP, EMA guidelines, ICH Q10, FDA 21 CFR Part 11 |
Batch records, CAPA, change control, data integrity |
Medical Devices |
FDA 21 CFR Part 820, EU MDR, ISO 13485 |
Design control, risk management, supplier quality, compliance |
Automotive/Aerospace |
IATF 16949, AS9100 |
Supplier quality, configuration management, change control |
Food & Beverage |
FSMA, EU food directives, ISO 22000/HACCP |
CCP monitoring, traceability, recall management |
High-Tech & Chemicals |
ISO 9001, IPC, REACH |
Process automation, change control, data integrity |
How to Choose QMS Software That Meets Your Industry Demands
Selecting the right QMS software is a critical decision that should align with your organization’s industry-specific requirements and business objectives. A life sciences company, for example, will have different needs than an automotive parts manufacturer, so the software chosen must be able to meet those unique demands. This section outlines a structured approach to evaluating and choosing QMS software, highlighting key factors to consider and how to ensure the solution will support compliance and performance in your particular industry.
Understand Your Industry Requirements: Begin by identifying the regulatory and operational requirements that your QMS software must fulfill:
-
List out all relevant regulations, standards, and guidelines your company must adhere to.
-
Determine any industry-specific workflows or terminologies that are must-haves. Good QMS software often comes with pre-configured process templates (for CAPA, audit management, change control, etc.), but these should be adaptable to your industry’s jargon and sequences.
-
Consider validation requirements. Especially in regulated industries (pharma, med devices), the QMS software itself may need to be validated to ensure it works as intended (a requirement under FDA guidelines for software used in quality systems). Ensure the vendor provides support for software validation (such as IQ/OQ/PQ protocols or documentation).
Key Criteria for Evaluating QMS Software Options: According to industry experts, there are several core criteria you should evaluate for any QMS software
-
Scalability: Can the software handle growth in users, sites, and data?
-
Integration: Does it integrate seamlessly with existing systems (ERP, MES, LIMS)?
-
Compliance Support: Does the solution align with regulatory standards (FDA, ISO, etc.)?
-
User-Friendliness: Is the interface intuitive, with role-based dashboards and mobile accessibility?
-
Customization vs. Configuration: Is the system flexible enough to be configured without expensive custom coding?
-
Vendor Expertise: Choose vendors experienced in your industry who offer strong customer support.
-
Total Cost of Ownership: Weigh licensing, implementation, and maintenance fees against long-term benefits.
Additional Considerations (Industry-Specific):
-
Validation for Regulated Industries: If you are in a regulated industry like healthcare, pharma, or med devices, ask how the vendor supports software validation. They should ideally provide a validation package or at least documentation of their Software Development Life Cycle (SDLC) and testing, to help you validate the system for use. Some companies prefer QMS software built on established platforms (e.g., Qualityze is built on Salesforce platform, which may offer reliability and security advantages).
-
Language and Localization: If operating in the EU or globally, check that the software supports multiple languages, date formats, etc., as needed. German manufacturers, for example, might want a German language interface for plant operators – some vendors provide translations.
-
Analytics and Reporting: Different industries have different key metrics (KPIs). Ensure the QMS software has robust reporting or BI integration so you can get insights relevant to your industry. For instance, a contract manufacturer might need to report ppm defects to customers; a pharma company might track batch release cycle time or complaint trending. Modern QMS often have customizable dashboards – verify that these can be configured to the metrics you care about.
-
Consider upcoming or recent changes in your industry regulations. For example, EU MDR (for devices) introduced new requirements; is the vendor actively updating the product to help clients comply (perhaps via built-in templates for MDR-specific processes)? Choose a vendor who is proactive on keeping up with industry evolution.
Shortlisting and Evaluation Process: With criteria in hand, the process might involve:
-
Research and shortlist 3–5 QMS vendors known in your industry (via market reports, referrals, case studies).
-
Engage each with a detailed RFP (Request for Proposal) outlining your requirements. Include industry-specific use cases for them to demonstrate.
-
Have them conduct demos/workshops with your team, ideally showing scenarios that matter to you (e.g., “show how a deviation->CAPA -> effectivity check process works in your system” for pharma; or “demonstrate how a supplier non-conformance is handled and linked to PPAP docs” for automotive).
-
Reference checks: Talk to some of their customers in your industry if possible to gauge satisfaction.
-
Ask the vendors pointed questions such as “How does your software support regulatory compliance?” and “What is the typical implementation timeline for a company of our size in this industry?” . The answers will reveal if they truly understand your domain.
A thorough selection process focused on industry alignment will pay off by resulting in a QMS platform that becomes an asset rather than a hurdle in your pursuit of quality and compliance.
Cost Considerations and ROI of QMS Software Based on Industries
Investing in QMS software involves significant cost, but it should be viewed in light of the return on investment (ROI) it can deliver through quality improvements, risk reduction, and efficiency gains. This section examines the components of cost for QMS software and how ROI can vary or be justified across different industries. We will draw on industry studies, white papers, and market data to quantify these aspects.
Components of QMS Software Cost:
-
Software Licensing/Subscription
-
Implementation Services
-
Training and Change Management
-
Maintenance and Support
-
Hardware/IT Infrastructure
-
Hidden Costs: There are often hidden costs of QMS implementation to be aware of :
-
-
Customization
-
-
-
Process Redesign
-
-
-
Data Cleaning
-
-
-
Data Migration
-
-
-
System Integration
-
-
-
Validation (in regulated industries)
-
ROI Drivers for QMS Software: The benefits of QMS software can be tangible (cost savings, less scrap) or intangible (improved brand reputation). Here are key ROI drivers and how they manifest in different industries:
-
Reduced Cost of Poor Quality: Lower scrap, rework, warranty claims, and recall expenses.
-
Efficiency Gains: Automation shortens process cycles and reduces labor-intensive manual tasks.
-
Compliance and Risk Mitigation: Prevents costly regulatory fines and production stoppages.
-
Enhanced Market Performance: Improved quality boosts customer satisfaction and brand reputation.
-
Faster Time-to-Market: Streamlined processes accelerate approvals and product launches.
-
Employee Productivity: Better training and process consistency reduce errors and improve efficiency.
Studies show that companies can see a 25% reduction in poor quality costs and substantial ROI—sometimes 300–500% over several years—by implementing a digital QMS.
Implement the Best QMS Software for Your Industry with Qualityze
Choosing QMS software is only part of the journey. Effective implementation is crucial to realize the benefits and ROI discussed. In this section, we outline best practices for implementing QMS software in an organization and highlight how a solution like Qualityze can support and streamline this process for various industries. Qualityze is used as an example of a modern QMS platform that is designed with multi-industry compliance in mind, illustrating features that facilitate successful adoption and improvement of quality management.
Here’s how Qualityze facilitates the process:
-
Industry-Focused Design: “Qualityze offers AI-Powered quality management software solutions that are designed with industry best practices in mind, catering to the requirements defined by regulatory bodies such as the FDA, ISO, and industry-specific standards.” This means that out-of-the-box, Qualityze comes with modules and workflows aligned to common standards (like CAPA aligned to ISO 9001 and FDA expectations, audit management aligned to ISO 19011 guidelines, etc.). For a company implementing QMS software, this reduces the time needed to configure the system to meet compliance – much is already built-in. For example, a med device company will find that Qualityze’s Nonconformance -> CAPA process can be quickly tailored to meet FDA QSR requirements.
-
Configurability and Flexibility: Qualityze provides a range of modules (Document Management, Change Control, Training, Supplier Quality, etc.) which can be turned on/off and configured as needed. This modular approach allows implementation in phases (you can implement core modules first, then add others). The Salesforce platform foundation of Qualityze ensures high scalability (capable of supporting large user bases and data) and reliable cloud infrastructure (with high uptime and security – important for global companies). Being on Salesforce also means integration capabilities (using APIs and connectors) are strong, facilitating linking Qualityze with ERP or other systems during implementation.
-
Compliance and Validation Support: Qualityze being ISO 9001:2015 certified itself indicates that the company follows robust processes. For regulated clients, Qualityze provides validation packages to help with the computer system validation process – this accelerates validation efforts. They also incorporate features like audit trails, electronic signatures, and role-based security to help clients meet Part 11 and other regulatory requirements. This heavy-lifting done by the software means during implementation, the team can focus more on process improvement and less on figuring out how to comply with electronic record rules.
-
User-Friendly Interface: Qualityze has a modern, web-based interface that looks and feels like familiar enterprise apps. This eases adoption. During implementation, companies have reported that users pick up the system quickly due to its intuitive design (navigation menus by module, dashboards of pending tasks, etc.). There is also the advantage of mobile accessibility – being cloud-based, users can access it from any site or device (given credentials), which is great for multi-site operations or field auditors.
-
Support and Community: Qualityze provides customer support and has a community of users. Their support team is available to assist through the implementation and after (with things like configuration questions, troubleshooting, etc.). Knowing that expert help is a call or click away can significantly smooth out the implementation journey.
-
Performance Improvements: The ultimate goal of implementation is to improve quality outcomes. Qualityze showcases aggregated results from its client base, such as “61% improved compliance, 36% faster audits and inspections, 50% reduced operational costs, 44% enhanced product quality and safety”. These figures, while from Qualityze marketing, give an idea of what effective QMS implementation can achieve. During your project, you can measure similar metrics to gauge success. For instance, after implementing Qualityze, you might track that audit findings have reduced by X% or training compliance is near 100% whereas before it was lower.
Conclusion
EQMS software has become a strategic necessity for industries facing strict regulatory and quality demands including pharmaceuticals, medical devices, automotive, aerospace, or food manufacturing, to drive efficiency, ensures compliance, and reduces costly errors.
By choosing a solution like Qualityze that fits your industry’s needs and implementing it with clear project management and change strategies, organizations can realize significant ROI and secure a competitive edge in today’s quality-driven marketplace.
Share
The Start of Something Amazing.
Request Demo
Products
Industries
Company