Table of Content
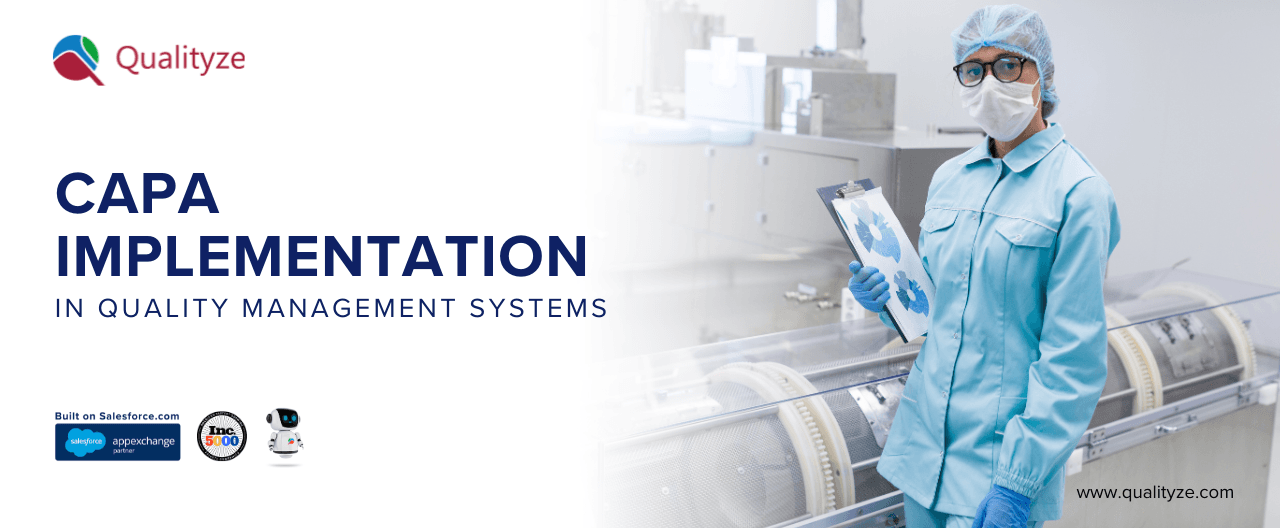
Corrective and Preventive Action (hereinafter CAPA) is indispensable to a robust and modern Quality Management System (QMS). Gone are the days when businesses searched for solutions after issues occurred. In today's world, it’s not only desirable but also necessary to prevent challenges before they escalate into an unmanageable crisis. Businesses across various industries rely on CAPA to predict, pre-empt, and address issues.
CAPA helps to increase quality of a product and reduce rework and recalls, making business operations cost-effective and efficient. It also helps exceed customer expectations by meeting regulatory requirements and eliminating standard lapses. Effective CAPA implementation within a QMS is crucial for meeting quality standards and minimizing risks. Qualityze CAPA management software is a comprehensive next generation AI enabled enterprise software solution designed to streamline and automate corrective and preventive action processes within quality management systems. It offers a range of features and benefits that make it a valuable tool for organizations seeking to improve product quality, regulatory compliance, and overall efficiency.
This blog discusses the key aspects of CAPA in QMS and how Qualityze CAPA software delivers quality. It also sheds light on its purpose, significance, and processes.
What is CAPA in QMS?
CAPA is a systematic approach used to identify, investigate and resolve the root causes of the issue within a QMS. It is a proactive quality management strategy that goes beyond simply fixing the problem. Its dual nature — corrective and preventive — ensures that organizations not only fix problems but also take proactive measures to prevent future occurrences.
Corrective action focuses on identifying and eliminating the root cause of a problem. The goal is to prevent the recurrence of the issue by addressing the underlying problem, not just its symptoms and should not be confused with correction action. Correction action involves in fixing the immediate problem, such as repairing a faulty product or replacing a defective part.
On the other hand, preventive action seeks to identify potential issue before they manifest as problems. By conducting a thorough risk analysis, organizations can prevent issues from occurring, thereby improving efficiency and safety.
Qualityze CAPA software, enhanced with AI capabilities, offers comprehensive solution to proactively identify and mitigate potential quality issues. By conducting thorough risk analyses, businesses can prevent problems before they arise, improving efficiency and safety.
AI-powered analytics provide deeper insights into data, enabling more precise risk identification and trend analysis.
Related Article: How to Avoid CAPA-Related Pitfalls on Your Compliance Journey
Where Does CAPA Fit into a Quality Management System?
CAPA integrates into all facets of a QMS, facilitating continuous improvement across all areas. Whether it’s production, service delivery, safety, customer complaints or compliance, CAPA helps identify non-conformances and ensures they are adequately addressed. CAPA connects to various aspects of QMS, such as document control, risk management, and change management, to provide a comprehensive approach to quality management.
The process typically begins with identifying an issue from an internal audit, customer complaint, regulatory requirement or emerging trends. This triggers the organization to assess the root cause of the problem, document the findings, and implement corrective and preventive measures.
In QMS, CAPA is a key component for continuous improvement, serving as the feedback loop that drives quality enhancement. From managing supplier quality to ensuring regulatory compliance, CAPA plays a role in every product or service lifecycle stage. Qualityze CAPA software supports a culture of continuous improvement by tracking trends and identifying areas for enhancement. It also maintains a comprehensive audit trail of all CAPA activities for regulatory compliance and traceability. The features that differentiate Qualityze CAPA software are:
- Cloud-based platform: It is a cloud-based solution that eliminates the need for on-premises infrastructure and reduces IT overhead, enabling easy accessibility from anywhere, anytime.
- Scalability: The software can accommodate organizations of all sizes, from small businesses to large enterprises, ensuring it can grow with your needs.
- Customization: It offers a high degree of customization, allowing you to tailor the system to your specific workflows and requirements.
- Integration: It seamlessly integrates with other Qualityze modules, such as Quality Management System (QMS) and Document Management System, providing a unified platform for managing quality-related activities.
- Regulatory compliance: It is designed to help organizations meet regulatory requirements, including those related to FDA, ISO, and other industry standards.
- Mobile accessibility: The software can be accessed on mobile devices, enabling you to manage CAPA activities on the go.
- Robust reporting and analytics: Qualityze CAPA provides comprehensive reporting and analytics capabilities, allowing you to track key performance indicators (KPIs), identify trends, and make data-driven decisions.
- AI Capabilities: Qualityze CAPA leverages AI to assist in identifying the root cause of a problem, analyze historical data to predict potential quality issues and proactively help implement preventive measures.
Related Article : CAPA by filtering - It’s not everything that requires a CAPA Management Process!
Importance of CAPA in Quality Management Systems
The importance of CAPA can never be overemphasized. It serves as the engine that drives compliance, safety, and quality in any QMS. Implementing effective CAPA procedures enables businesses to meet regulatory requirements, maintain customer trust, and ensure product safety. CAPA also contributes to operational efficiency by reducing waste, improving processes, and preventing costly mistakes. Qualityze CAPA software builds operational efficiency by:
- Nonconformity management: Creates, tracks, and help investigate and resolve nonconformities, optimizing results and eliminating waste.
- Root cause analysis: Assist in conducting thorough root cause analyses to identify the underlying causes of an issue leveraging several quality tools.
- Corrective action planning: Develop and implement effective corrective actions to address nonconformities.
- Preventive action planning: Implement preventive actions to prevent similar issues from recurring.
- Document management: Stores and manage all relevant documents related to CAPA activities.
- Workflow automation: Automates workflows to streamline processes and reduce manual effort.
- Effectiveness Review: Conduct evaluations of the implemented action plans to assess the effectiveness of the CAPA process.
In regulated industries, CAPA is often a requirement under standards like ISO 9001 and ISO 13485. Regulatory bodies such as the FDA expect organizations to have CAPA processes. Failure to comply can result in legal consequences, product recalls, or reputational damage.
Beyond regulatory compliance, CAPA offers intrinsic benefits to organizations. It reduces the risk of recurring issues, helps organizations allocate resources more effectively, and improves customer satisfaction. By solving problems at the root, CAPA improves long-term performance, making it an essential tool for achieving operational excellence.
Why Implementation of CAPA is Necessary for QMS
Implementing CAPA is necessary for several reasons. First, it helps organizations identify underlying problems before escalating into more significant ones. By addressing these concerns proactively, businesses can reduce downtime, avoid costly recalls, and enhance customer satisfaction. Additionally, CAPA contributes to risk management by identifying potential risks and implementing mitigation measures.
CAPA Process of ISO 9001
ISO 9001 sets the standard for QMS, and its CAPA process is central to continuous improvement. The ISO 9001 CAPA process typically follows a structured approach, which includes identification, root cause analysis, implementation of corrective actions, and monitoring.
The first step is to identify the non-conformance. This could arise from internal audits, customer complaints, emerging trends or product failures. Once identified, the next step is to investigate and analyze the root cause. This is critical because merely addressing the symptoms of the issue won’t prevent its recurrence.
After identifying the root cause, corrective actions are implemented to resolve the problem. These actions must be documented, and their effectiveness monitored over time. Preventive actions should also be considered to mitigate future risks. Finally, the CAPA process involves reviewing the results and making necessary adjustments to the system. ISO 9001 emphasizes documentation and review to ensure that CAPA actions are effective and sustained.
ISO 13485 CAPA Management System
ISO 13485, the international standard for medical device quality management, places significant emphasis on CAPA. In industries like medical devices, the consequences of quality failures can be dire, making CAPA a compliance requirement and a critical safety measure.
The CAPA process in ISO 13485 follows a similar approach to ISO 9001 but with more stringent requirements due to the nature of the medical device industry. It involves documenting issues, conducting risk analysis, implementing corrective and preventive actions, and monitoring effectiveness. ISO 13485 also requires organizations to maintain detailed records of their CAPA activities to demonstrate compliance during audits.
One key difference between ISO 9001 and ISO 13485 CAPA is the focus on risk management. ISO 13485 requires organizations to assess non-conformances' impact on patient safety and product performance. This means that corrective and preventive actions must be evaluated for their immediate effectiveness and long-term implications on safety and compliance.
Related Article: How to Ensure Successful CAPAs?
Corrective Action vs. Preventive Action
Corrective and preventive actions are two sides of the same coin in CAPA but serve different purposes. Corrective action is reactive; it addresses an issue that has already occurred. For example, if a batch of products fails quality testing, a corrective action would involve identifying the root cause and implementing measures to prevent recurring issues.
Preventive action, on the other hand, is proactive. It aims to identify potential issues before they occur and implement strategies to prevent them. For instance, if a risk assessment identifies a potential failure point in a production process, preventive action would involve adjusting the process to mitigate that risk. Qualityze CAPA software identifies and manages risks associated with nonconformities. It also facilitates collaboration among team members and stakeholders. The AI-powered Qualityze CAPA software leverages predictive analytics to analyze historical data and predict potential nonconformities, enabling proactive measures to be taken.
Both corrective and preventive actions are crucial for a successful CAPA process. While corrective action fixes problems after they happen, preventive action helps organizations avoid potential issues, reducing risk and improving overall quality. Together, they form a comprehensive problem-solving and risk management approach within a QMS.
Conclusion
Effective CAPA implementation is fundamental to maintaining and improving any organization's quality management systems. Whether under ISO 9001 or ISO 13485, CAPA ensures compliance, promotes continuous improvement, and mitigates risks. By understanding the differences between corrective and preventive actions, businesses can address issues more effectively and proactively prevent future problems. Implementing CAPA within a QMS enhances operational efficiency and helps meet regulatory requirements, ensuring long-term success.
Share
The Start of Something Amazing.
Request Demo
Products
Industries
Company