Table of Content
1 Significance of Quality Management
2 How to Ensure Proper Quality Controls in Automotive Industry?
1. Streamline Supplier Quality-Related Processes
2. Standardize Parts/Components Inspections
3. Establish Effective CAPA Management System
4. Manage Complaints Efficiently
5. Perform Regular Audits
6. Manage Equipment Calibration and Maintenance Schedules
7. Provide Best-Practices Training to Your Workforce
8. Manage Controlled Documents and their Changes
9. Report Nonconformance in a Timely and Streamlined Manner
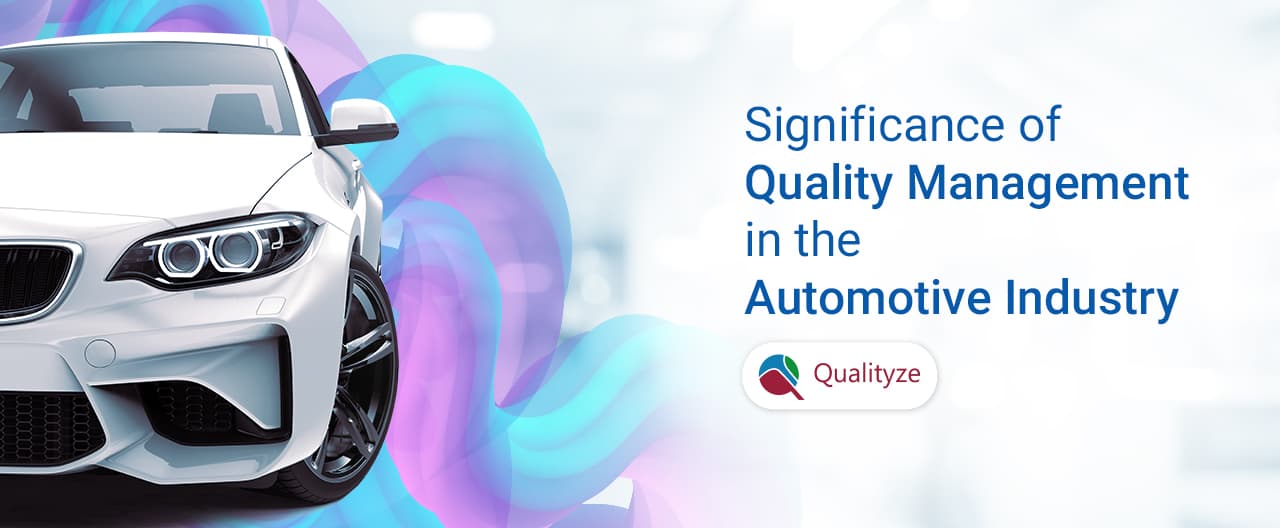
Quality management is important in almost every industry. It helps organizations to ensure product quality and compliance before it gets delivered to the customers.
The automotive industry is one that has witnessed more challenges than any other industry.
You must be thinking about why quality management is crucial for making automotive parts and components? And what can quality managers do to improve the processes and controls in their business units to ensure high-quality products?
Significance of Quality Management
Quality management is important for automotive manufacturers and suppliers to deliver products that meet quality and compliance standards. It may seem expensive, at first, to manufacture high-quality products, but it can save you money in the long run. In the automotive industry, products without proper quality management can trigger costly recalls, while a defective product can cause an accident and pose a threat to drivers.
Always remember, “Quality is remembered long after the price is forgotten.”
A closed-loop quality system helps identify issues before a product is marketed to consumers, resulting in a better product release. It also drives a culture of continuous improvements throughout the organization. With the proper quality processes and controls in place, you can ensure that these products comply with industry standards – for some products, like the exhaust and emissions systems, compliance is essential.
Related Articles: Effectively Managing Automotive Quality through Qualityze EQMS
How to Ensure Proper Quality Controls in Automotive Industry?
Ensuring proper quality controls in the automotive industry would require you to;
1. Streamline Supplier Quality-Related Processes
Product quality starts right from the suppliers. You must streamline supplier quality-related processes to ensure that you are doing business with the right people. For this, you can also utilize an advanced supplier quality management solution that can help you with every process, from supplier qualification checks to data integration for improved decision making. The new-age software solutions also help improve collaboration and communication with the suppliers, strengthening the business relationships.
The automotive companies that analyze and streamline their supplier-related processes can adapt to market changes much quickly while achieving operational excellence. Are your supplier processes streamlined yet?
2. Standardize Parts/Components Inspections
Maintaining consistency in the automotive industry can be a challenge due to the wide variety of products, production methods, and testing requirements. A robust Inspection Management software can be of assistance here. With software, you can streamline the incoming, in-process, and outgoing inspection processes. You can also ensure the quality of incoming materials by standardizing sampling plans across different components and products. Make sure you choose a software solution with an intuitive and configurable interface to simplify and streamline inspections.
The automotive companies that standardize the inspection processes are likely to prevent catastrophic events and unnecessary expenses from a product recall.
3. Establish Effective CAPA Management System
Nonconformances are common in quality management. You must have a well-defined CAPA management process to manage defects and deviations that could impact the product quality. An effective CAPA management solution can help automotive companies to identify the root cause of the problem efficiently and eliminate them so they do not reoccur. The next-generation CAPA management software can be easily integrated with the existing business applications to give you more visibility through the product failure trends and develop an action plan accordingly.
Establishing an effective CAPA management system can help you take a holistic approach to systemic issues.
4. Manage Complaints Efficiently
Automotive companies that want to sustain their business relationships should have an effective complaints management system in place. The software manages and implements the entire complaint lifecycle, including documenting the problem, performing root cause analysis, responding to customers immediately, and triggers internal and external corrective and preventative actions. Make sure you chose a cloud-based complaints management solution that enables you to collect data from all the resources to resolve quality issues effectively and efficiently.
Automotive companies that have a compliant and standardized complaints management system in place are likely to build lasting business relationships with their customers, suppliers, and stakeholders.
5. Perform Regular Audits
To maintain quality standards in the automotive industry, companies should implement Audit Management software to perform and manage external and internal audits. It is important to choose a software solution that provides IATF 16949 compliance to make organizations audit-ready. The software should provide you greater flexibility to schedule yearly, half-yearly, quarterly, and ad hoc audits flawlessly in advance. It should be effective to perform online and offline audits within the system.
Make sure the audit management software you chose comes with configurable workflows so you can manage different types of audits without any hassles.
6. Manage Equipment Calibration and Maintenance Schedules
Equipment calibration and maintenance are crucial to measurement and testing during the manufacturing, assembly, and service stages to ensure excellent performance. You can utilize a Calibration/Maintenance Management Solution to schedule regular calibration and maintenance programs for your equipment to provide the required accuracy and precision. In addition, it helps the organization remain compliant while sustaining success. The next-generation cloud-based solutions enable you to standardize the calibration/maintenance process cycle without any hassles.
The automotive companies can significantly improve the overall equipment efficiency, i.e., speed, usability, and quality while reducing the unpredictable and expensive production downtime with regular calibrations and maintenance activities.
7. Provide Best-Practices Training to Your Workforce
In today’s work environment, training is an essential part of staying on top of all certifications that the organization requires. An effective training management system enables organizations to identify training needs within different departments and monitor the results of all training, including documents read and signed off, assessments, and instructor-led training. An organization can also release certificates based on employee performance.
Automotive companies should emphasize employee competency through effective training programs to ensure that they follow best practices to achieve the organization’s quality objectives.
8. Manage Controlled Documents and their Changes
Automotive companies can rely on a Document Management System to manage all their critical documents from creation to approval, publishing to archiving, and erasing them permanently. With the software solution, you can schedule approvals, archival, and document management well in advance. Users and organizations can work together to review documents. The software also comes with alerts and notifications capability to notify users of the changes done.
9. Report Nonconformance in a Timely and Streamlined Manner
Identifying the nonconformities and product issues during the inspections and quality control process is important to develop an appropriate action plan and maintain product quality. Automotive companies should have a proper system for nonconformance reporting and tracking. They can also utilize nonconformance management software that enables them to document all the nonconformances with the necessary details in a simplified and compliant manner.
Sounds like too much effort. Right?
What if you can manage all these processes using a single solution?
Yes, you heard it right. One single-stop solution for all your automotive quality management needs, i.e., Qualityze EQMS Suite for Automotive Industry. You can bid adieu to all the challenges associated with the traditional approach, including disconnected systems, traceability & visibility issues., compliance issues, and a lot of paperwork.
Through easy-to-configure, predefined workflow templates, the Qualityze Enterprise Quality Management Solution helps you meet your quality, compliance, and regulatory requirements. We provide a complete EQMS solution that integrates all the quality processes. Our solution comes with Advanced Reporting & Dashboard Capabilities, E-Signature, Email Approval, Centralized Database, and much more to reduce process cycle time.
Related Article : Quality Standards: Transforming the Automotive Industry Landscape
To get more details about Qualityze Enterprise Quality Management Software, get in touch with our customer success team on 1-877-207-8616 or write to us at info@qualityze.com, and we will be right there for you.
Share
The Start of Something Amazing.
Request Demo
Products
Industries
Company